Introduction:
Fly ash is a fine powder that is produced from the gases emitted by coal-fired power plants. This substance is commonly used as a byproduct in thermal power stations that utilize crushed coal as fuel, due to its significant pozzolanic activity. By incorporating fly ash into the production of fly ash-lime blocks, a supplement to traditional burnt earth blocks, natural resources can be preserved and ecological quality can be improved.
To make fly ash-lime bricks, a mixture of fly ash, lime, and an accelerator is used. Crushed base debris or sand may also be added to the mixture when required. The mixture is then shaped into blocks and subjected to curing cycles at various temperatures and pressures. The crushed base debris or sand is used as a coarser material to regulate water retention in the final product. When fly ash reacts with lime in the presence of moisture, it forms a calcium silicate hydrate, which acts as the binder material for the fly ash-lime blocks. Consequently, fly ash-lime blocks are chemically bonded blocks that can be used in brickwork construction similar to traditional burnt earth blocks.
The production of fly ash-lime building blocks has been initiated in many countries, and it is anticipated that this trend will continue on a large scale. This standard specifies the basic requirements for fly ash-lime blocks to achieve consistency in their manufacturing process. By utilizing this resource, we can contribute to sustainable development and minimize environmental damage.
Properties of Fly Ash Bricks:
- Fly ash bricks have an attractive appearance with a uniform and smooth cement color, and they do not require plastering for construction purposes.
- In terms of thermal conductivity, they have the ability to block heat and reflect a significant amount of light.
- These bricks also provide excellent sound insulation, making them a good choice for reducing noise pollution.
- They are highly resistant to fire and pests, and have the ability to withstand attacks from both.
- Additionally, fly ash bricks are highly durable and can last a long time, while only absorbing 6-12% of the water they come in contact with. This results in walls that are less humid and more resistant to moisture damage.
Environmental Effects:
The use of fly ash in cement manufacturing can have positive environmental effects.
- One such benefit is the reduction in the need for natural resources such as clay, sand, and limestone.
- By incorporating fly ash, the amount of cement required is also reduced, which in turn results in a decrease in carbon dioxide emissions during the manufacturing process.
- Furthermore, fly ash utilization can also help conserve agricultural land by reducing the need for topsoil in activities like brick manufacturing and landfill.
- Finally, it’s worth noting that fly ash can enhance the strength of concrete products without increasing the amount of cement required.
Advantages of using fly ash bricks:
Fly ash bricks offer numerous benefits compared to traditional bricks. They have improved work-ability, reduced permeability, and reduced heat of hydration. Additionally, they exhibit high sulfate resistance, increased long-term strength, high chloride corrosion resistance, greater resistance to alkali reactivity, and better concrete finish. Furthermore, fly ash bricks exhibit reduced shrinkage, and improved work-ability, which makes them an excellent choice for various construction projects.
Uses of Fly Ash Bricks:
Fly ash bricks are versatile and can be used in various construction projects. They are often used to make load-bearing exterior walls for small and medium-sized buildings, as well as for internal walls that must hold weight. In addition, fly ash bricks are an excellent choice for high-rise buildings that need to support a lot of weight. While they cannot replace burnt clay bricks entirely, fly ash bricks are an excellent alternative and can be used in factories, power plants, warehouses, and multi-story structures.
Scope of making Fly Ash Bricks as a Business:
The production of fly ash bricks is a lucrative business opportunity that can yield substantial profits. These bricks are in high demand within the construction industry, making them an ideal investment.
Fly ash brick production has proven to be a successful enterprise, with many small towns and villages now manufacturing and distributing them nationwide. Furthermore, fly ash bricks are an excellent alternative to traditional red bricks. The government is even promoting the use of fly ash bricks as an Eco-friendly alternative to red bricks, which are harmful to the environment during their manufacturing process.
This business has tremendous potential for stability and growth. Investing in an automatic fly ash brick-making machine can significantly reduce labor requirements while increasing production output. Overall, making fly ash bricks is an excellent business venture with a bright future.
Raw Materials Required:
- FLY ASH: The primary component of raw materials for fly ash bricks is fly ash, which predominantly influences the properties of the finished product. Since fly ash is non-plastic, it is necessary to include a binding agent such as plastic clay or Portland cement. Typically, fly ash content ranges from 60% to 80%.
- LIME: For the binding agent, it is advisable to use high calcium lime with adequate strength. This lime component reacts with silica and alumina present in fly ash, forming a binder under aqueous conditions. However, partially burned lime is not preferred as it sets too quickly. Lime particles should be finely ground to ensure complete dispersion and coating of the mixture’s grains.
- Gypsum: An industrial waste, is also a necessary component in the fly ash brick-making process. It can be procured from fertilizer plants, where it is available as industrial waste.
- Sand or crusher dust can be added as an economizer to slightly increase brick strength. Locally sourced sand is commonly used. Alternatively, crusher dust can replace sand and serves as an equally effective substitute.

Manufacturing Process:
- The process starts with the loading of raw materials into the batching plant using a mini loader. The raw materials are then automatically weighed based on preset weights using load cells and control circuitry. If cement is available in bulk, a silo and screw controller are used to automatically weigh it. Otherwise, the batching is programmed to use one bag of cement.
- Once the materials are weighed, they are mixed in a twin shaft mixer, which blends the mixture homogeneously and intimately in a semi-wet form. Water is automatically added according to a set time, and the twin shaft mixer ensures that the perfect mix is achieved in the shortest possible time.
- Next, the mix is carried to the casting machine via a conveyor belt. The automatic brick-making process is achieved using a series of operations controlled by an automatic PLC system. The pallet is pulled into the machine, and the mix is fed into the machine molds. A T boggy uniformly spreads the materials in the molds, after which automatic PLC-controlled vibration and hydraulic pressure are applied for a while, resulting in perfectly compacted and high-quality bricks.
- The freshly cast bricks, along with their pallets, are then automatically stacked using a pallet stacker. The final stack of 5 to 10 pallets and bricks is lifted with a forklift and carried to the drying bay/room for initial setting.
- After the initial setting, the blocks/bricks are stacked for curing in layers. The layers are stacked to enable water and air to go all around, ensuring proper curing and drying. The curing process continues for seven days, after which the blocks/bricks are allowed to dry for a day before being ready for dispatch. Alternatively, the blocks/bricks can be steam-cured for eight hours or mist-cured for 24 hours immediately after production and then dispatched.
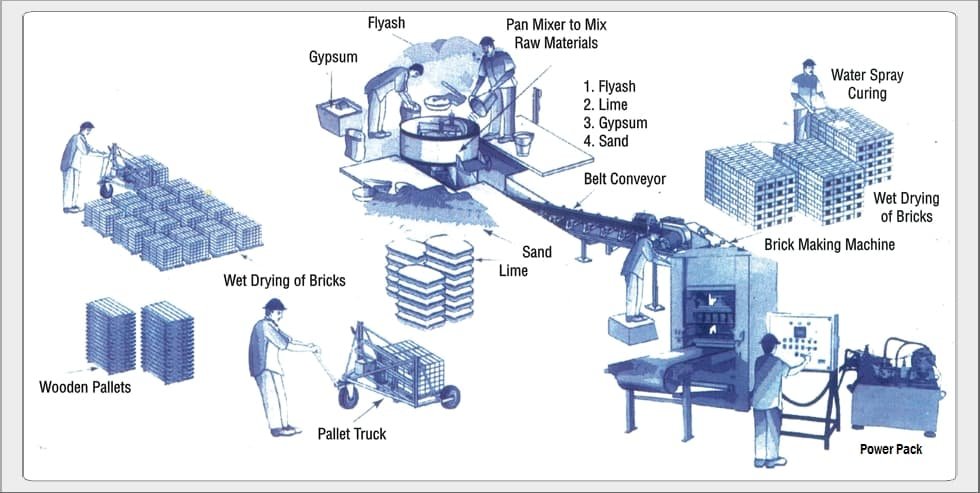
In summary, the process involves loading of raw materials, automatic batching, mixing, automatic brick-making, automatic stacking, forklift shifting, curing, and dispatching of the cured bricks to the market.
Space & Staff Required:
The amount of land required for a business to produce bricks from fly ash is determined by the machine’s hourly output. The land area typically ranges from 10,000 to 12,000 square feet. The brick-making process necessitates 5 to 20 laborers, who can manufacture between 3,000 and 20,000 bricks in an 8-hour shift.
Location: When starting a fly ash brick manufacturing business, it is essential to choose a location with easy access to raw materials, labor, and machines. Adequate electricity supply is also necessary. Therefore, the location of your business does not matter, as long as all of the aforementioned amenities are readily available.
Staff: To operate a fly ash brick-making business, a minimum of 5 to 10 laborers is required to manage machine operations, load and unload raw materials, and carefully store bricks after shaping them.
License Required:
Obtaining licenses is crucial when starting a fly ash brick-making business, as the industry necessitates a complete machinery setup. You can apply for a license by submitting an application form to your local authority and can expect to receive it promptly. The necessary documents for starting a fly ash brick-making business include:
- Aadhar card
- PAN card & address proof
- MSME license
- GST registration
- Shop and Establishment license
- Trade Mark (if required)
- NOC from the state pollution control board
Business Profit:
The profitability of a business depends on its supply; the more units sold, the greater the revenue. However, profits in any business are not constant as the cost of raw materials may fluctuate. Therefore, it is difficult to set an exact profit margin for the fly ash brick-making business. The price of fly ash bricks varies from Rs 5-10/piece, depending on the location. If the monthly supply of bricks is high, one can expect to earn a good profit of approximately 3 to 5 lakh and more.
Marketing:
Effective marketing is crucial for the success of any business. Hence, it is imperative to ensure that your business has a strong marketing presence in your locality. One way to achieve this is by collaborating with truck/tractor drivers, masons, builders, and local cement shops, as they can help drive up your sales. Additionally, posting advertisements about your business in their respective locations can also be beneficial. To further enhance your business growth, you can explore other marketing strategies as well.
Where to buy machine?
Machines for producing bricks from fly ash are available in various models, with the capacity to produce between 500 and 10,000 bricks per hour. The cost of a fly ash brick-making machine starts at 1.5 lacs. This environmentally friendly project does not cause pollution, and various state governments offer subsidies to encourage its adoption.
You can buy all the machine which is required to start Fly ash brick manufacturing business from your local manufacturer or explore different model of machinery on HYPKO or you can directly contact on +91 9770111233 (Er. Anubhav Chauhan, Co-owner: HYPKO) to get knowledge about the machinery.
Risks involved in the business:
As a newcomer to the business world, it is essential to understand the various risks associated with it.
These include:
- Ensuring that you have a comprehensive plan in place for your business.
- Understanding the needs and requirements of your staff and customers.
- The possibility of incurring losses due to low demand in your local market.
- Facing production stoppages due to machinery-related issues.
- Having adequate staffing levels to maintain manufacturing operations in the event of absences.
- Maintaining a positive attitude and persevering through difficult situations.
Conclusion:
Starting a brick-making business is a lucrative venture since bricks are a highly utilized construction material. If you have a well-crafted and sustainable business plan for producing bricks, market competition should not be a major concern.
To succeed in this business, your focus should be on creating top-quality, resilient, and robust bricks. It is essential to have a clear understanding of your business objectives, such as its profitability, production costs, and scale.